预测性维护在铝型材机架加工设备中的应用:减少停机,保障交期
在铝型材机架加工行业中,设备的稳定运行是保障生产计划与订单交付的。传统的定期维护和故障后维修模式存在停机时间长、维护成本高的问题,而预测性维护通过数据驱动的前瞻性管理,正在成为提升设备可靠性的关键技术手段。
技术原理与价值
预测性维护基于物联网(IoT)传感器、大数据分析和机器学习算法,实时采集设备运行数据(如振动、温度、压力、电流等),结合历史维护记录构建故障预测模型。通过对关键参数的趋势分析,系统可提前识别异常征兆(如刀具磨损、传动系统疲劳、液压泄漏等),定位潜在故障点,并推荐佳维护窗口。相较于传统维护模式,其价值在于将被动维修转变为主动干预,减少非计划停机时间50%以上。
典型应用场景
1. 挤压机健康管理:通过监测主缸压力波动与油温变化,预测密封件老化或油路堵塞风险,避免因突发停机导致挤压生产线中断。
2. CNC加工中心刀具寿命预测:利用主轴电流和振动频谱分析,动态评估刀具磨损状态,优化换刀周期,减少加工精度偏差造成的返工。
3. 传动系统智能诊断:在辊道输送设备中部署加速度传感器,检测轴承磨损特征频率,提前2-3周预警故障,避免连带性机械损伤。
实施路径与效益
企业需分阶段构建数字化维护体系:首先部署边缘计算设备实现数据实时采集,其次通过云平台建立设备数字孪生模型,终形成自适应优化的预测算法。某铝材企业应用后,设备综合效率(OEE)提升18%,年度维护成本降低30%,订单准时交付率从82%提升至96%。
未来展望
随着5G和AI技术的融合,预测性维护将向自愈式维护演进。通过工艺参数与设备状态的闭环优化,铝材加工设备将实现真正的智能化运维,为行业可持续发展提供坚实保障。
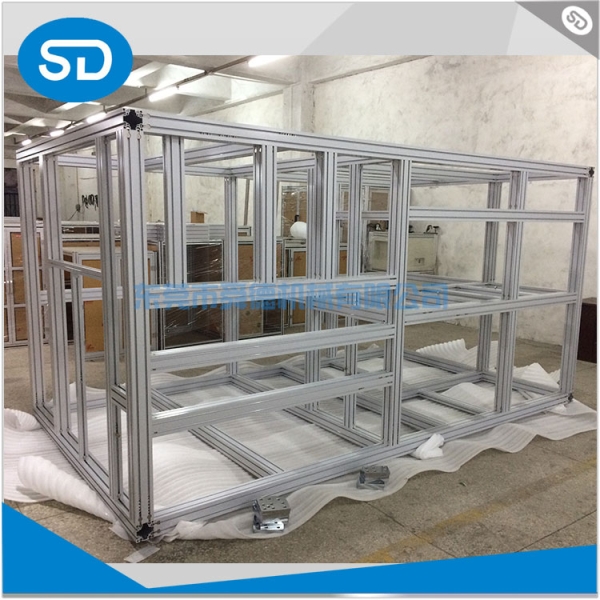