铝型材机架轻量化设计的极限挑战:拓扑优化与仿生结构融合
在工业装备轻量化趋势下,铝型材机架设计正面临突破性技术挑战。传统减重手段已逼近材料性能极限,而融合拓扑优化与仿生结构的新型设计范式,为铝合金框架的极限轻量化开辟了新路径。
拓扑优化通过构建应力传递路径,颠覆了经验式设计逻辑。基于有限元分析的迭代算法可识别冗余材料区域,在保证刚度的前提下实现减重率突破30%的跃升。但纯数学优化生成的复杂晶格结构面临制造可行性瓶颈,这正是引入仿生结构的战略价值所在。自然界亿万年进化形成的骨骼孔隙结构、竹纤维分布、蜂巢拓扑等生物力学模型,为工程优化提供了兼具性与可制造性的原型参考。
两者的深度融合需要多学科交叉技术壁垒:首先需建立生物结构特征参数与力学性能的量化模型,通过机器学习筛选仿生模板;其次须开发面向增材制造的拓扑优化算法,将仿生结构的梯度密度特征融入设计约束;要突破传统挤压工艺限制,开发复合3D打印与数控加工的新型制造体系。德国某机床企业通过模仿甲虫鞘翅的复合腔体结构,成功将五轴加工中心框架重量降低42%,同时提升动态刚度18%。
这种技术融合正推动轻量化设计进入"自然-数字"双驱动时代。随着生成式设计算法与多尺度技术的进步,未来铝型材机架有望实现比强度突破100MPa·cm³/g的生物级轻量化水平,为装备的能效革命提供支撑。
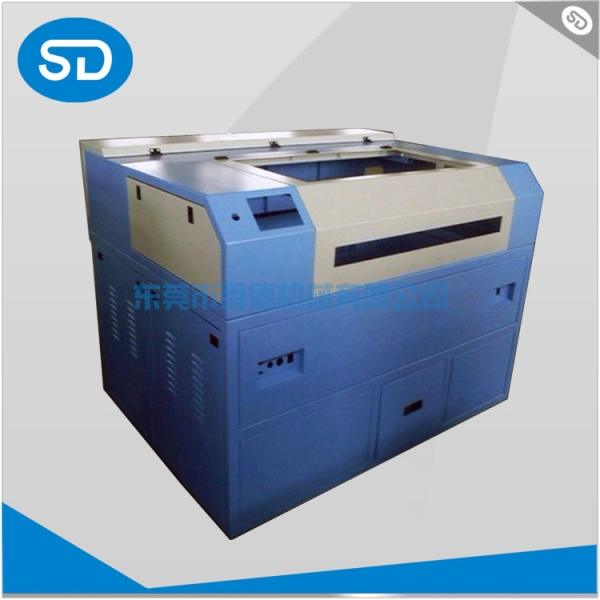