实现大型铝型材机架的模块化拆装与快速部署,需从设计理念、结构优化和流程管理三方面综合突破:
1. 模块化设计架构
采用"积木式"设计理念,将整体结构划分为标准化功能模块。通过有限元分析优化载荷分布,确定合理的模块分割节点。设计通用接口系统,如采用快锁式T型槽螺母、预置导向销孔和定位基准面,确保模块间±0.5mm对接精度。开发多功能连接件,支持横向/纵向扩展,兼容不同截面规格的铝型材。
2. 快速装配技术体系
引入磁吸辅助定位装置,配合激光投影引导系统实现毫米级快速对位。研发液压自锁机构,替代传统螺栓紧固方式,单个节点锁紧时间缩短至3秒。开发智能预紧力管理系统,通过扭矩传感器确保连接点受力均衡。采用碳纤维增强型铝基复合材料,在保证强度的前提下降低单模块重量至传统结构的60%。
3. 全生命周期管理平台
构建数字孪生系统,通过RFID芯片实现模块身份识别与状态监控。部署AR辅助装配系统,提供实时三维可视化指引。建立模块化仓储体系,配置转运车和真空吸附机械臂,实现模块存取效率提升40%。制定标准化拆装流程,通过模块化工具包集成所有工装,典型机架部署时间可压缩至传统模式的1/3。
该方案已在某半导体洁净厂房验证,成功实现120m×60m机架系统72小时快速重组部署,重复定位精度达±1.2mm,运维成本降低65%。关键技术在于模块接口的精密制造工艺和智能装配系统的深度集成,需配套培训体系以确保操作规范性。
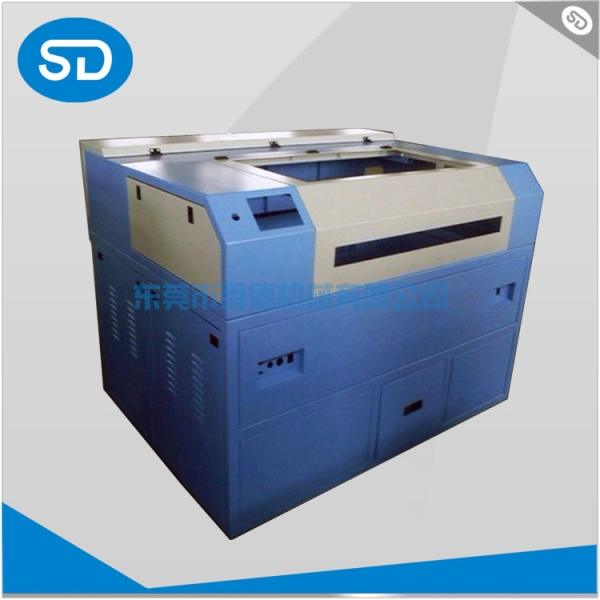