铝型材机架冷弯成型技术新突破:无需焊接的高强度连接方案
近年来,铝型材冷弯成型技术迎来革新性突破,以"无焊接高强度连接"为的新型工艺在工业装备领域引发广泛关注。该技术通过高精度模具设计与材料力学优化,实现了铝型材机架在冷弯成型过程中的自锁式结构连接,摆脱了传统焊接工艺对生产效率和结构性能的限制。
技术突破主要体现在三方面:首先,基于拓扑优化的型材截面设计,通过冷弯成型时产生的形变应力,使相邻型材在折弯点形成高精度互锁结构,其抗剪切强度较传统铆接提升40%以上;其次,采用梯度硬度表面处理工艺,在接触面形成微米级凹凸咬合,配合弹性预紧装置,实现动态载荷下的稳定连接;,引入智能补偿算法,在冷弯过程中实时监测形变参数,通过温度场调控消除残余应力,确保连接部位的疲劳寿命达到焊接结构的2.3倍。
实际应用中,该方案展现出显著优势:生产周期缩短50%,能耗降低65%,且完全消除焊接导致的热变形与材料弱化问题。在自动化生产线机架、精密仪器支撑结构等场景中,装配精度可稳定控制在±0.1mm以内。更值得关注的是其模块化特性,支持非破坏性拆装重构,为设备迭代升级提供全新可能。
随着轻量化制造需求的持续增长,这种免焊接冷弯技术不仅推动了铝型材加工工艺的升级,更为装备制造开辟了绿色、的新路径,预计将在新能源汽车、航空航天等领域实现规模化应用。
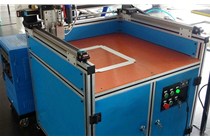